Recipe Preperation
| Raw materials used in high and medium amounts in the production formula are generally weighed on a weighing pan using various feeders. Additives that are present in small amounts in the formula are prepared by weighing them more precisely. Additive weighing can be done semi-automatically or fully automatically. The prepared mixtures are fed to the mixer or other production machines such as dissolver and extruder by being drawn with its own flow or vacuum pneumatic conveying method, depending on the process and factory layout. However, raw materials in high and medium amounts can also be dosed using a weighed vacuum system. This ensures that raw materials in different places within the facility are fed to the same point.
The PLC automation system controls the recipe preparation system, which is designed in a variety of ways and specifically for the application, according to the needs of the project, the characteristics of the process and the amount of raw materials used. Thanks to programming that enables automation and production scenarios to meet all needs, and SCADA software that controls the facility by the operator, production is continued precisely and at the same quality.
VOLDE prescription preparation system solutions;
- Fully automatic weighing of main raw materials and additives
- Weighed vacuum transport system
- Manual additive weighing
- Continue dosing system
- Volumetric and gravimetric feeders
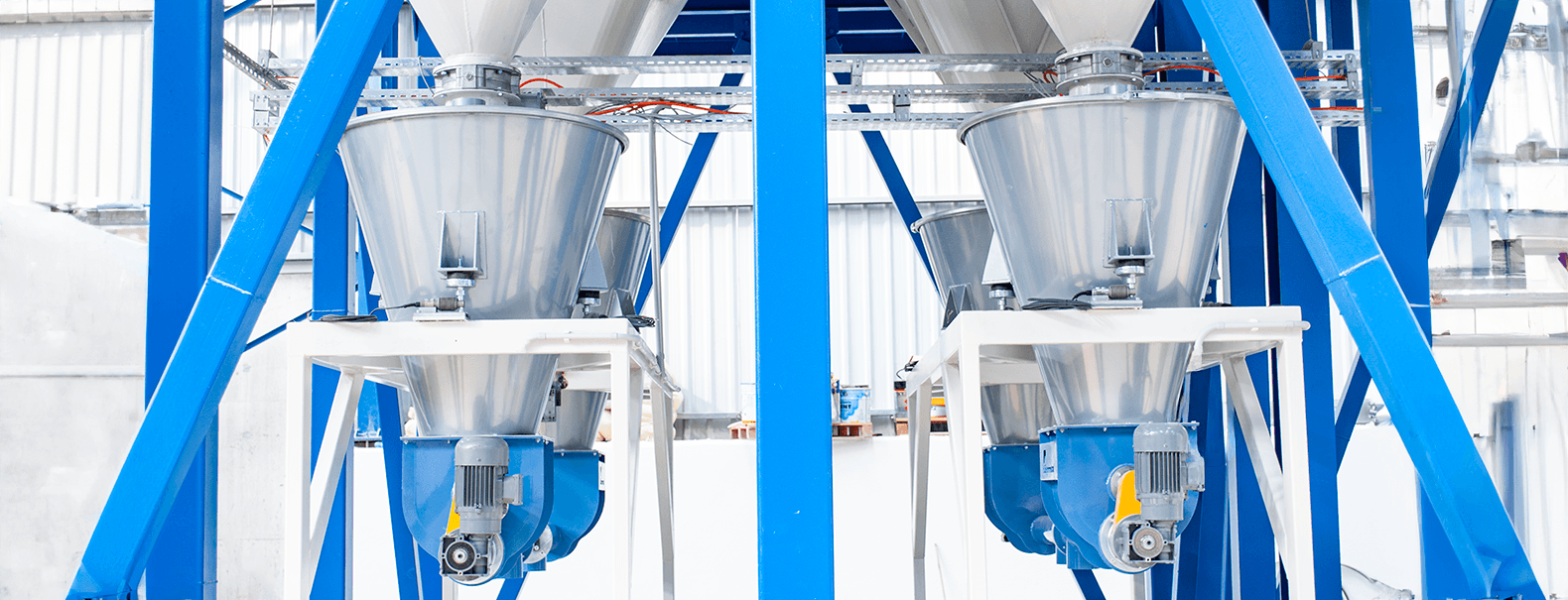
Weighing of Main Ingredients
Batch Dosing
| Raw materials to be used in large quantities in the system are stored in silos or bunkers. Depending on the structure of the material, screw feeders, belt feeders or vibrating feeders are used in feeding equipment. When dosing raw materials, the quantities are measured with weighing pans with precision scales. The entire operation is managed using a control system, ensuring that the exact amount of each raw material is dosed according to the specified ratio. After the raw materials are weighed, they are usually discharged into a blender. The homogeneously mixed material coming out of the mixer is transferred to production machines via conveying systems such as screw conveyors, belts or pneumatic systems.
| With automatic dosing systems, the same amount of raw material is used in each batch, ensuring that the production quality is constantly same. In addition, these systems increase efficiency and make the production process faster compared to manual processes. The possibility of human error, often encountered in manual measurements, is significantly reduced. Additionally, the computerized nature of these systems facilitates traceability, making it easier to document and track batches, quantities, and raw material usage. VOLDE automatic weighing and dosing systems have the capacity to integrate with Enterprise Resource Planning (ERP) or Manufacturing Execution Systems (MES). This integration enables seamless production planning, inventory management and advanced quality control.
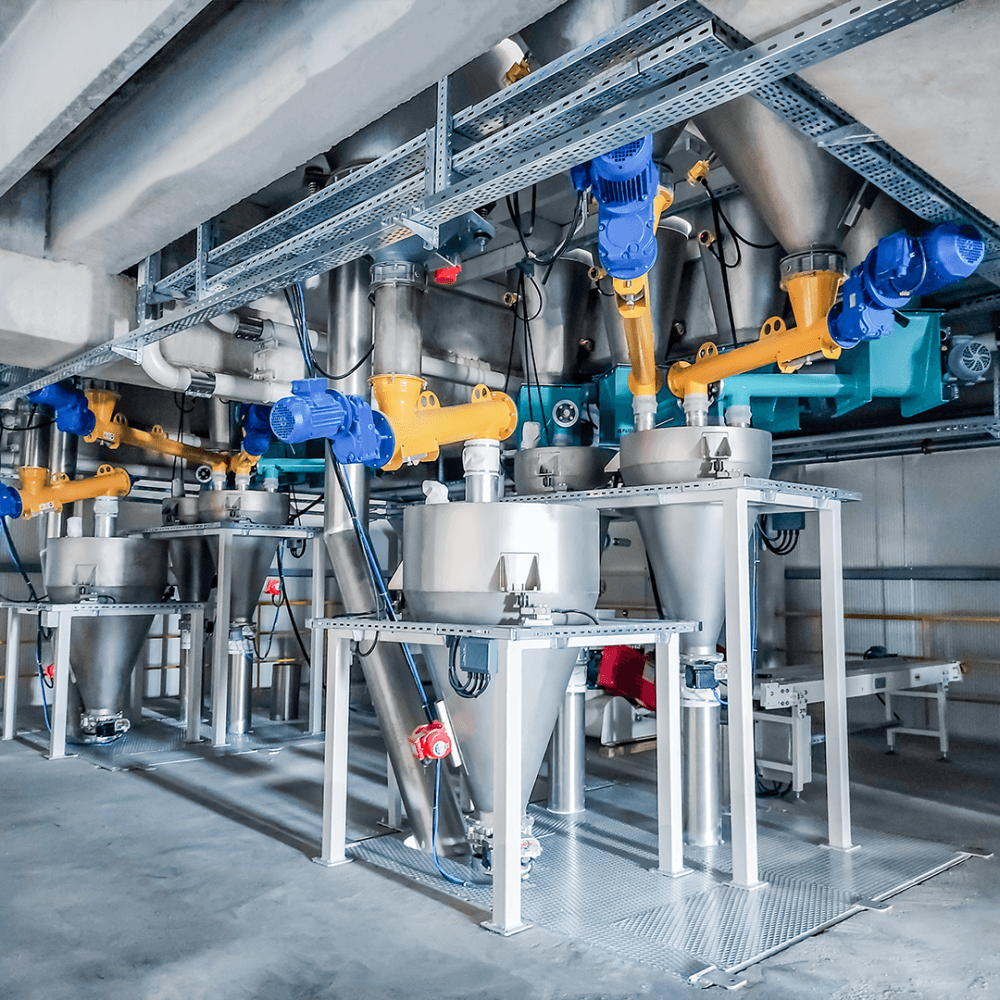
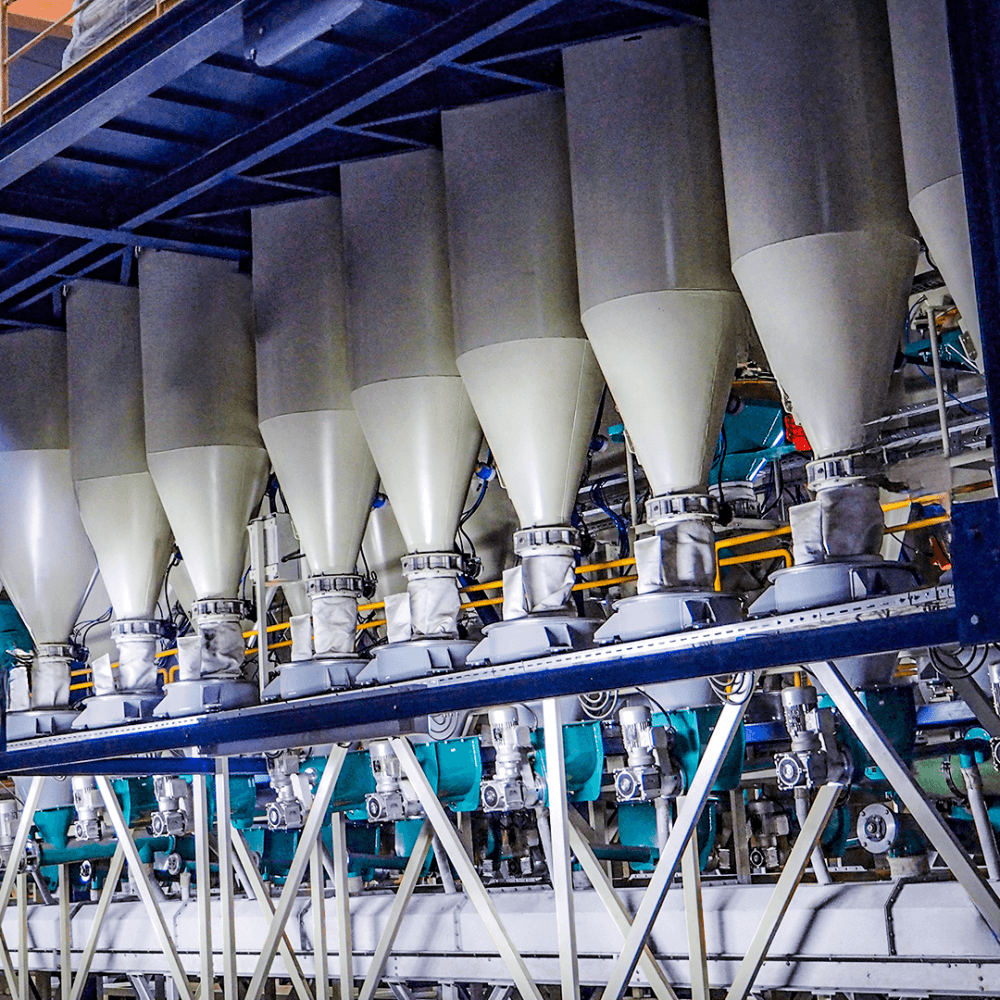
Continue Dosing
| In continue dosing systems, the flow amount of ingredients is kept constant and is ensured to flow at the same flow rate at the set capacity without interruption. These systems are designed by VOLDE especially for high capacity and continuous production processes. In continue dosing systems, each ingredient in the formula is fed uninterruptedly and since each works at a constant discharge capacity (kg/h), the mixing ratio remains constant. VOLDE Loss in Weight feeders are the most important equipment used in these systems. In this system, which is installed before the continue mixer or extruder, other additive materials in certain proportions are added with Loss in Weight Feeders while it is flowing onto the main material, which generally passes through a collection conveyor, creating a homogeneous sandwich structure with the same content in each section.
Minor Ingredients Weighing
| In practical applications, minor additives used in formulations are measured and added to the main product using semi-automatic or fully automatic systems. These additives, typically included in production using 25 kg capacity bags, are stored with the help of bag dumping bunkers and are weighed using suitable dosing devices. Designed according to the specific requirements, the following systems are utilized
- Manual weighing stations
- Semi-automatic dosing units
- Fully automatic dosing systems
These systems ensure that the minor additives are prepared with the utmost precision to complete the recipe. The purpose of micro-dosing is to enhance product quality, reduce labor costs, and provide precise control over the processes.
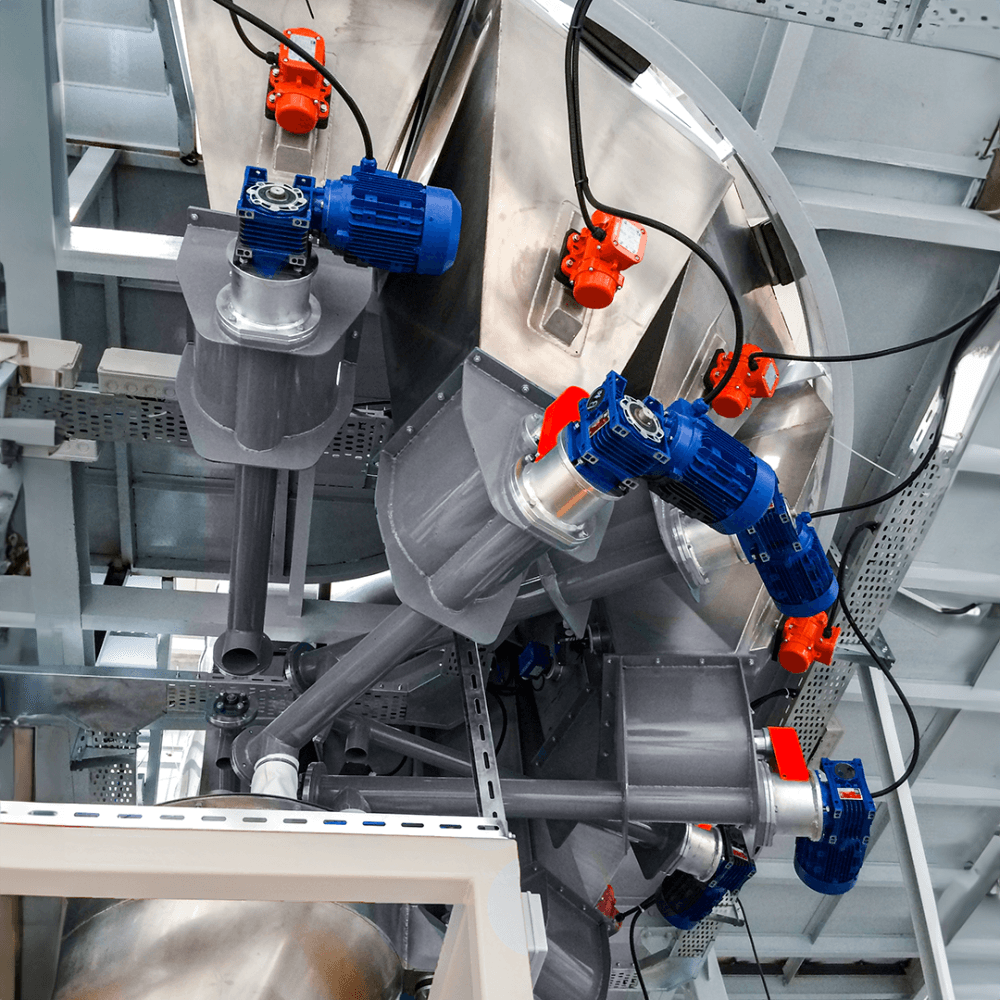
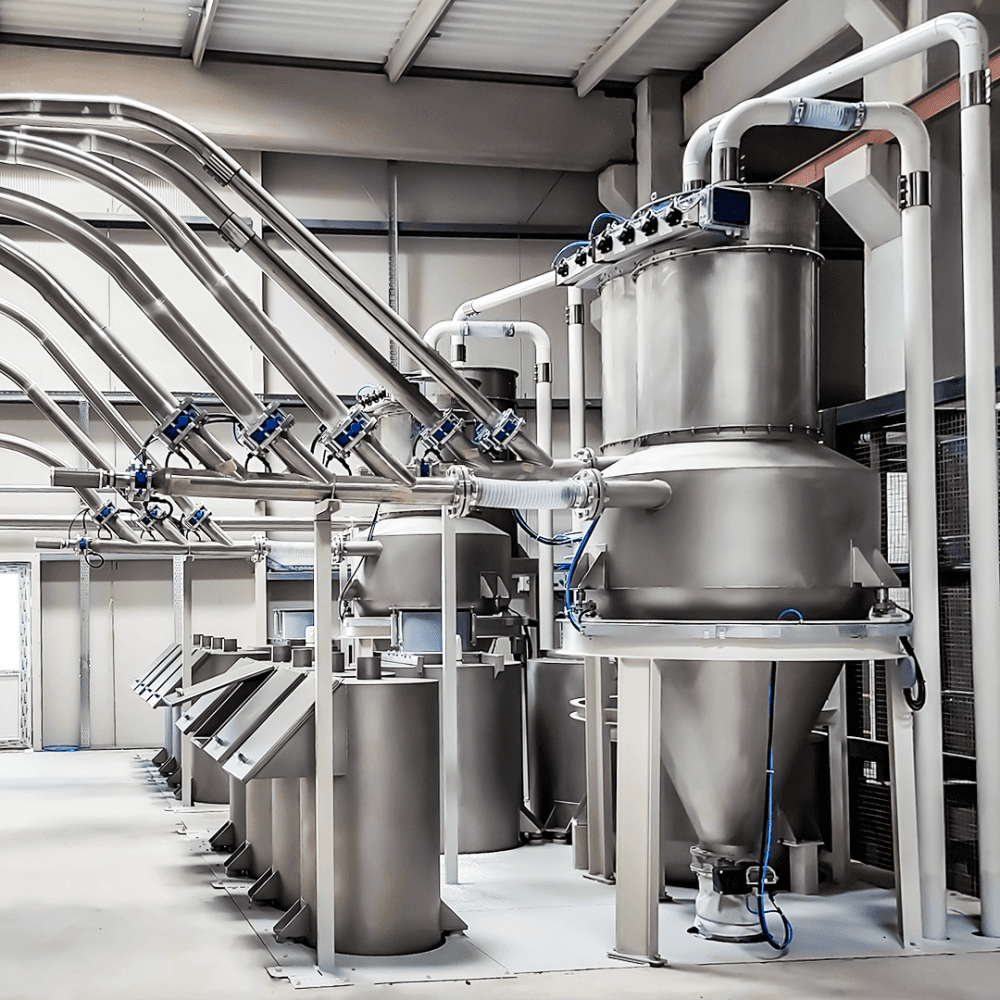
Weighed Vacuum Conveying
| In dosing systems, the weighing process of various raw materials in the desired kg values can be done with various feeders in batch or continuous mode. Alternatively, the weighing process can also be performed while conveying the raw material pneumatically with a vacuum. This method is generally preferred for the majority of materials in a formulation, and it is a suitable solution for materials stored in silos. Thanks to VOLDE's experience and expertise in this field, it ensures the desired capacity and dosing precision even in the finest powders, and establishes more precise and practical facilities.
Process Automation
| Process automation is a critical technology used to enhance the efficiency and safety of industrial processes. These systems utilize automatic devices and software to monitor, control, and optimize facility operations. Process automation makes production processes more precise, reduces the likelihood of errors, enhances worker safety, and optimizes energy costs. Additionally, it provides continuous improvement opportunities through data collection and analysis. Here is the critical role that process automation plays in the industrial world, supporting operational excellence while increasing productivity.
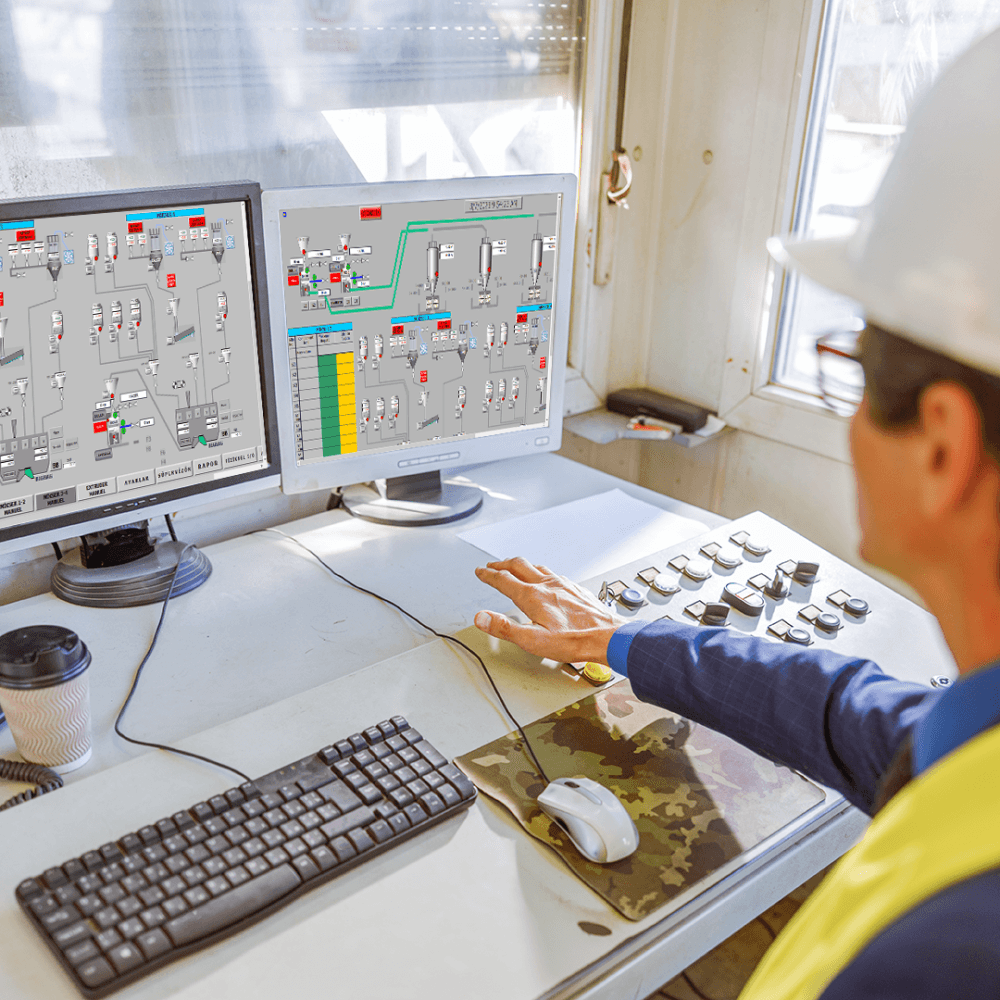